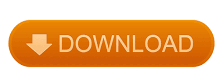
Operate the knock out pins in a uniform fashion.
Make the thickness of the molded product uniform. Residual stress from the molding process is released, causing deformation. The molded product warps immediately following or at some time following molding where the mold cavity should be straight. Increase the cavity internal pressure (secondary pressure). Same as what causes voids, but sink marks arise when the surface cools too slowly. The surface of the molded product collapses somewhat-something that is particularly common in thicker products. Change the gate locations so as to prevent air intake. To enhance strength, add several thick, uniform reinforcement ribs to the product design. Change the product design so that the thickness is no greater than 6 mm.
Lower the cylinder temperature setting.Air gets trapped within the molten polymer, leaving bubbles within the product.In molded products with a thickness greater than 6 mm, voids are very difficult to avoid. As a result, the polymer is pulled outward, causing all shrinkage to concentrate in the thickest parts of the product leaving holes within the product. The surface of the molded product loses heat rapidly through the mold wall and the polymer hardens.Change in density as the material changes from a molten to a coagulated state.The presence of holes inside molded products Ⅱ. Choose a low-viscosity high flow type material.Change the gate locations so that the weld lines occur in locations less susceptible to external forces if weld strength is an issue.Provide a cold slug well where weld lines occur.Material splits and flows in separate directions, then converges again.This results in reduced strength, as well as burn-mark and bubble defects. When the divergent flow fronts converge again, hair-like lines appear where they meet. The material splits off and flows in two or more directions. Investigate for potential contamination.
#Winject injection failed reason 5 install#
Install an ultrared light inside the hopper. Increase (or decrease) the size of the runners and gates. Thoroughly clean molding machine cylinders. Apply back pressure to generate a kneading effect. Material is contaminated with another type of material. Streaks of a silvery white color appear in the material flow direction. Create more distance between the gates and the location of the mold coolant. Increase the gate cross section surface area. Once that molten polymer starts to coagulate, it gets pushed by the molten polymer injected afterward and forms miniature bands. The molten polymer cools rapidly within the mold and becomes highly viscous. Ring shaped miniature bands appear on the molded product surface around gates or narrow sections. Choose a low-viscosity high flow material type. Add ribs to the molded product design to improve flowability. Increase gate cross section surface area. If the nozzle clogs frequently, raise the mold temperature or shorten the cycle time. Make sure there are no severed lines to the heater. Raise the cylinder temperature setting. Install a screw with a back-flow check valve. If material feed is still insufficient at maximum material feed capacity, change to a larger capacity machine. Gate cross-section surface area is too small. Insufficient injection-molding machine performance (shot capacity, plasticizing capacity, etc.). DescriptionĪ molded product that is incomplete because the mold cavity was not filled completely. AMILAN™ Nylon Resin Technical Information|Injection-molding|Common injection-molding defects and their countermeasures Short shot or short molded Ⅰ.